Luoyang launches full bearing series for world’s largest ring rolling mill
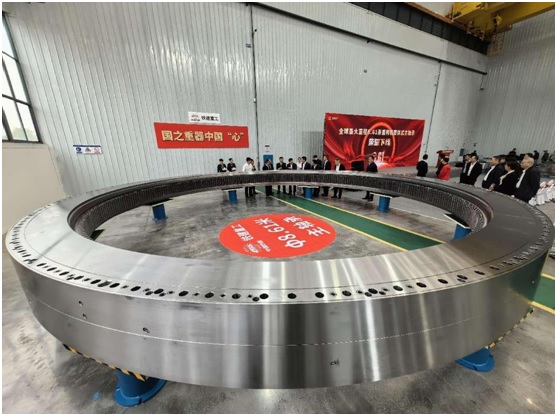
Henan Daily
Zhengzhou’; On July 9, Luoyang Bearing Group Co.,Ltd. achieved a manufacturing milestone by producing the complete bearing series for the world’s largest ring rolling mill. This breakthrough not only fills a critical gap in ultra- large, ultra-heavy-duty forging components in China, but also establishes the country as a global leader in high- end bearing design and manufacturing.
Bearings, often referred to as the “industrial joints”, are fundamental components of mechanical equipment and play a critical role in determining manufacturing capabilities. The ring rolling mill is a key to produce massive metal rings, and the precision, load-bearing capacity, and reliability of its bearings dictates the nation’s ability to build major equipment.
The ring rolling mill they support marks China’s first domestically developed system of its class, capable of forging 22-meter-diameter rings under 3,552-ton rolling forces. Pushing industry limits in scale and load capacity, these bearings represent a major technical breakthrough, featuring exceptional complexity, high development challenges, and uncompromising reliability demands.
Ling Hong, chief engineer of the Large-Scale Bearing Division at Luoyang Bearing Group, introduced that the bearings rolled out this time feature newly developed structures, including semi-cage retainers and split raceways, innovations that overcome mega-scale engineering challenges. The bearings are made from newly developed materials with exceptional resistance to heavy loads and deformation, enabling them to withstand extreme rolling forces and impact loads under harsh working conditions. In addition, specially optimized heat treatment processes endow the bearings with excellent wear resistance, fatigue strength, and extended service life. These combined advantages ensure the stable operation of the ring rolling mill’s core components while significantly reducing maintenance costs for end users.
At the same time, the R&D team pioneered innovative machining techniques and inspection methods, propelling the bearings to world- class geometric and rotational accuracy, ending foreign dominance in high-end bearing technologies.