Italy: Scientists may have found magic ingredient behind ancient Rome’s self-healing concrete
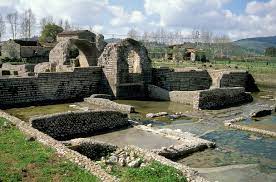
Rome: The ancient Roman Empire still makes its presence felt throughout Europe. Bathhouses, aqueducts, and seawalls built more than 2000 years ago are still standing—thanks to a special type of concrete that has proved far more durable than its modern counterpart. Now, researchers say they have figured out why Roman concrete remains so resilient: Quicklime used in the mix may have given the material self-healing properties.
The work could help engineers improve the performance of modern concrete, says Marie Jackson, a geologist who studies ancient Roman concrete at the University of Utah, but who was not involved with the research.
The Romans were not the first to invent concrete, but they were the first to employ it on a mass scale. By 200 B.C.E., concrete was used in the majority of their construction projects. Roman concrete consisted of a mixture of a white powder known as slaked lime, small particles and rock fragments called tephra ejected by volcanic eruptions, and water.
Modern concrete, in contrast, is typically made from Portland cement: a mixture of limestone, clay, sand, chalk, and other ingredients ground and burnt at scorching temperatures. It also starts to crumble in as little as 50 years.
Scientists have previously tried to explain why Roman concrete is so long-lasting. In 2017, for example, researchers found that—at least for structures exposed to the ocean—seawater reacted with the ingredients of the concrete, creating new, tougher minerals.
But were there other explanations? To find out, Admir Masic, a chemist at the Massachusetts Institute of Technology, and colleagues gathered concrete samples from an ancient city wall in Privernum, a 2000-year-old archaeological site near Rome. Back in the lab, they focused on small calcium deposits embedded in the concrete known as lime lumps.
Other scientists had speculated that these tiny chunks were simply a result of the Romans mixing their concrete poorly. But Masic and his colleagues wondered whether they were instead caused by the Romans using quicklime in their mix before setting it with water. The widely available white powder, made from burning limestone, would have reacted with water during mixing, sparking a chemical reaction that produced significant amounts of heat. This would have prevented the lime from fully dissolving, resulting in the lime lumps.
And indeed, when the researchers tried to make their own Roman concrete in the lab with quicklime, they ended up with material that was “identical” to the samples they gathered from Privernum, Masic says.
When the team created small cracks in the concrete—as would happen as the material aged—and then added water (as would happen with rainwater in the real world), the lime lumps dissolved and recrystallized, effectively filling in the cracks and keeping the concrete strong, the researchers report today in Science Advances. “This has an incredible impact,” Masic says.
Modern concrete typically doesn’t heal cracks larger than 0.2 or 0.3 millimeters across. The team’s Roman-inspired concrete, in contrast, healed cracks up to 0.6 millimeters across.
Masic hopes the work will inspire today’s engineers to improve their own concrete, perhaps with quicklime or a related compound. Indeed, he says, a startup concrete company plans to employ the new discovery. The material wouldn’t just be less expensive than current self-healing concrete, Masic says, it could also help fight climate change: Cement production accounts for 8% of greenhouse gas emissions.
“Romans made extremely intelligent decisions based on excellent empirical observations,” Jackson says. “The more we can learn from ancient construction technologies, the better.”